The 15th (2015) Yamazaki-Teiichi Prize Winner Material
Contribution to the development and application of creep-strength-enhanced ferritic heat resistant steels and highly efficient power plant operation
Winner | ||
---|---|---|
Fujimitsu Masuyama | ||
History | ||
Mar. 1970 | Completed Master’s Course, Department of Metallurgy, Graduate School of Engineering, Kyushu Institute of Technology | |
Apr. 1970 | Joined Nagasaki R&D Center, Technical Headquarters, Mitsubishi Heavy Industries, Ltd. | |
Mar. 1988 | Doctor of Engineering, Osaka University | |
Apr. 2001 | Executive Advisory Engineer and Principal Researcher, Nagasaki R&D Center, Technical Headquarters, Mitsubishi Heavy Industries, Ltd. | |
Apr. 2003 | Professor, Department of Applied Science and Integrated System Engineering, Graduate School of Engineering, Kyushu Institute of Technology | |
Apr. 2009 | Specially-appointed Professor, Department of Applied Science and Integrated System Engineering, Graduate School of Engineering, Kyushu Institute of Technology | |
Apr. 2012 | Specially-appointed Professor, Department of Materials Science, Graduate School of Engineering, Kyushu Institute of Technology | |
Present |
Winner | ||
---|---|---|
Atsuro Iseda | ||
History | ||
Mar. 1982 | Completed Master’s Course, Department of Metallurgy, Graduate School of Engineering, Osaka University | |
Apr. 1982 | Joined Central Research Laboratories, Sumitomo Metal Industries, Ltd., | |
Jun. 1991 | Doctor of Engineering, Osaka University | |
Jul. 1991 | Assistant Manager, Pipe & Tube Works, Sumitomo Metal Industries, Ltd. | |
Apr. 1995 | Technical Manager, Chicago Office (USA), Sumitomo Metal Industries, Ltd. | |
Apr. 1999 | Section Manager, Specialty Tubular Technology & Quality Control Department, Pipe & Tube Works, Sumitomo Metal Industries, Ltd.; Became General Manager in June 2006 | |
Oct. 2012 | General Manager, Specialty Tubular Products Technical Service & Solution Department, Pipe and Tube Division, Nippon Steel and Sumitomo Metal Corporation | |
Present |
Reason for award
Active efforts have been made to improve the efficiency of thermal power generation in order to reduce CO2 emissions and thereby prevent global warming. The most effective way to raise efficiency is to improve heat-resistance of the heat-exchanger tubes in coal-fired power boiler and heat recovery steam generator of gas turbines combined cycle. Therefore, it is essential to develop heat-exchanger tubes with high creep strength at elevated temperatures, as well as superior resistance to oxidation and thermal fatigue.
Fujimitsu Masuyama and Atsuro Iseda have co-studied for many years on these issues, and in this case they optimized steel tube chemical compositions, microstructure, normalizing and tempering conditions, and thereby developed four new types of creep-strength-enhanced ferritic heat-resistant steels with outstanding creep strength, corrosion resistance, toughness, and ductility, as well as significant material cost reduction. Furthermore, by conducting detailed metallographic investigation of the creep damage processes of steel tubes using a transmission electron microscope and other tools, they have clarified the deterioration mechanism of heat-resistant steels under high temperature and pressure, and achieved stable, safe, and long-term operation of boilers by establishing highly accurate technology for evaluation of service life.
Improved efficiency of thermal power generation due to the development of these steels contributes to a reduction in CO2 emissions of several hundred million tons every year worldwide (annual CO2 emissions for all of Japan are about 1.3 billion tons), and it is expected that these contributions will continue in the future.
For above reasons, Dr. Masuyama and Dr. Iseda have been awarded the 15th Yamazaki-Teiichi Prize in the Material field.
Background of research and development
At present in Japan, operation of nuclear power plants is facing difficulties, and thermal power accounts for about 90% of the electric power supply. Stable supply of power is the most critical issue for supporting the national energy infrastructure, and thus the power companies are planning to greatly expand thermal power. Almost all of this will be coal-fired. With coal-fired power, it is essential to increase temperature and pressure in the steam conditions in order to reduce CO2 emissions and protect the environment, and this requires economical steels with outstanding heat-resistance. It is also essential to use high-strength ferritic heat-resistant steels with superior economy to increase the temperature of heat recovery steam generators in gas turbine combined cycle systems employing natural gas, which have low CO2 emissions among thermal power systems but high fuel costs. There is a strong need for evaluation, diagnosis and service life assessment based on elucidation of long-term material behavior of heat-resistant steel, to enable high-efficiency operation over the long term at higher temperatures.
Achievements
In this work, the researchers developed four types of economical creep-strength-enhanced ferritic heat-resistant steels suited to the operating conditions of boilers for thermal power generation. Steps were then carried out to achieve international standardization of the materials developed in Japan including these four steels, and to develop material technologies for service life evaluation. In this way efforts were made to realize large-scale practical use. The details of this work were as follows:
1) Development of creep-strength-enhanced ferritic heat-resistant steels
Low-carbon 9Cr-2Mo steel is a material in which the amount of carbon is reduced to approximately 0.06%, and the content of Mo, a solute strengthening element, is increased to 2%. Its distinguishing feature is that, in order to strengthen carbide precipitation of the ferrite structure, Mo is added at a rate of 2% to compensate for the reduction in solute Mo due to precipitation of Mo carbide in conventional steel containing 1% Mo, and in this way solute strengthening is maintained. Due to these strengthening mechanisms, strength of this material at 600℃⁄100,000 hours increased from the 35 MPa level of conventional steels to the 60 MPa level.
With regard to 12Cr-1Mo-1W-V-Nb steel, severe corrosion with steel of small-diameter tubes in furnaces for what (at the time) were heavy-oil-fired and black-liquor-fired soda recovery boilers was dramatically improved, based on the successful design of the above steel material, by adopting 12% Cr with comparatively low carbon of 0.1% for 12% Cr steel. At the same time, creep rupture strength of this steel at 600℃⁄100,000 hours was raised to the level of austenitic stainless steel by adopting a composition of 1%Mo, 1%W with addition of V and Nb, and performing high-temperature tempering at 800℃.
12Cr-0.5Mo-2W-V-Nb-Cu steel is a material in which the aforementioned 12% Cr steel developed and made practical for use in small-diameter tubes was improved for better toughness and higher strength to enable use in large-diameter, thick-walled pipe. It is extremely difficult to achieve a martensitic single-phase structure while retaining the heat-resistance of 12% Cr steel with 0.1% carbon, and the amount of Cr was reduced somewhat (11% Cr), and Cu was used as an alloy element for realizing an austenite single-phase at the normalizing temperature. Use of Cu with this kind of material is unprecedented, and this is an extremely original alloy design. As a result, the material achieved a creep rupture strength at 600℃⁄100,000 hours of approximately 130 MPa, and ultra-supercritical power plants were realized using this material.
0.06C-2.25Cr-0.1Mo-1.6W-V-Nb-B steel was developed through the initiation of research to apply the composition design of Gr. 91 (modified 9Cr-1Mo steel developed in the U.S.), which is currently used in large quantities, to conventional 2.25Cr-1Mo steel. Stimulated by the discovery that strength increases with lower levels of carbon, a high creep strength rivaling that of Gr .91 was obtained by adding 1.6%W, V, Nb, B and adjusting trace elements. Figure 1 shows the above two types of steel used in the main steam headers of a coal-fired ultrasupercritical power plant.
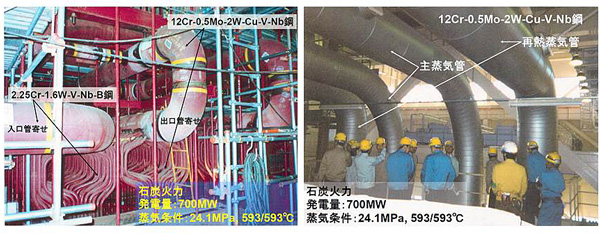
Fig. 1 Two types of developed steel used in critical pressure parts of a 700MW coal-fired ultrasupercritical power plant.
2) International standardization
The boiler and pressure vessel codes and standards (including nuclear power) of the American Society of Mechanical Engineers (ASME) have worldwide authority in this field, but previously there have been no coverage in this codes and standards for materials developed in Japan. Due to action by the committee members, the latter two of the above four types of developed were incorporated into ASME codes and standards together with other materials developed in Japan, and thereby achieving international standardization.
3) Development of material technologies for evaluating service life
When heat-resistant steel is used for a long time at high-temperature in power generation equipment, creep damage occurs and service life is reduced, but previously there has been no knowledge whatsoever regarding the cause-effect relationship between structural changes and mechanical damage in that process, and there has been no technology for non-destructive evaluation of service life, including the early and mid-life stages prior to the occurrence of mechanical damage. Therefore, metallographic analysis was carried out on deteriorated and damaged materials used for a long time to ascertain the cause-effect and transient degradation mechanism from structural changes to mechanical damage, and phenomena newly found as a result of this analysis were used to evaluate service life. That is, in the process where the Mo element in the M6C carbide (M=Mo+Fe), which precipitates out due to a carbide reaction in Cr-Mo steel, migrates from the solute Mo in the matrix, sulfur is concentrated onto the interface between the M6C and the matrix, and this causes interface separation which becomes the start of cavitations and micro cracks. By modeling the steps of this fundamental damage process, an original and completely new metallographic technique was developed for non-destructive evaluation of service life.
Meaning of the achievements
1) Four types of ferritic heat-resistant steels were developed, with markedly superior creep strength as materials for high-temperature equipment in thermal power plants and optimal characteristics for current service conditions. Large-scale practical application has been achieved in power plants inside and outside Japan through field demonstration tests. In particular, 2.25Cr-1.6W-V-Nb-B steel has opened the way for worldwide practical application not only in coal-fired power, but also as an indispensable material for improving economy and raising temperature of heat recovery steam generator in gas turbine combined cycle systems employing natural gas.
2) Of the developed steels mentioned above, and standardized in Ministry of Economy, Trade and Industry (METI) standards for thermal power generation technology and in European TÜV standards, two steels achieved international standardization through code coverage in ASME boiler and pressure vessel codes and standards, which the primary authority worldwide. As a result, these materials have come into practical use, as an international standard material, in high-efficiency thermal power generation in countries throughout the world.
3) The principles of material deterioration behavior were clarified for heat-resistant steels used at high temperatures for a few decades or more as the material of high-temperature equipment for thermal power generation, and based on those findings, a metallographic method for evaluating service life (included in the guidelines of the Agency of Natural Resources and Energy) was developed and made practical.
Due to these advances in development and practical application, a major contribution was made to improving efficiency of thermal power generation and achieving safe, long-term operation, and this is extremely significant for contributing to a stable supply of electric power, not only in Japan but also throughout the world. In particular, with a gas turbine combined cycle using the developed 2.25Cr-1.6W-V-Nb-B steel for the heat recovery steam generator, it is possible to reduce fuel usage and CO2 emissions by about 25%, and thus a major contribution can be expected from the perspective of improving efficiency and protecting the global environment.