The 1st (2001) Yamazaki-Teiichi Prize Winner Material
Next Generation, Electrical Resistance Welded Steel Tube with High Strength and Excellent Formability Contributing to Energy Conservation
Winner | ||
---|---|---|
Takaaki Toyooka, Motoaki Itadani, Akira Yorifuji, Yoshikazu Kawabata, Yasue Koyama, Mikio Kodaka |
||
Affiliation at the time of the award | ||
Technical research Loboratories, Kawasaki Steel Corp. |
Background of research and development
Owing to the limits on both global resources and related purification ability, effective utilization of limited resources and preservation of the global environment will be necessary henceforth. At COP3 in Kyoto in 1997, the resolution was made to substantially reduce carbon dioxide emissions. In keeping, to raise mileage, the automotive industry has been promoting lightweight bodies through the use of high-strength materials, along with the improvement of engines. However, the problem was that in general, the strength and formability of steel are inextricably linked; thus, if steel is given high strength, it loses the desired formability. Moreover, conventional methods for strengthening steel involve the addition of various alloy elements, but when steel was used as scrap, various problems arose, including the fact that the desired properties could not be obtained and recycling was hindered. Thus, there has been great desire for the development of high-strength, high-formability, environmentally sound eco-materials that can solve these problems.
Achievements
- 1) Features of HISTORY (high speed tube welding and optimum reducing technology) tube developed As shown in Figure 1, HISTORY tube was manufactured by heating electric resistance welded (ERW) steel tube and using a stretch reducer to conduct warm-reducing. Conventionally, stretch- reducing was done by hot-reducing (900-1100°C), since deformation resistance is low within the hot-range. However, with this research, as shown in Figure 2, by rolling steel in the warm-range ¡Ê650¡Á900°C¡Ë, of which the rolling load is in fact several times what it is in the hot- range, microstructure and texture control as indicated in Figure 3 was conducted. This made it possible to manufacture from a single material, high-function steel tube covering everything from high strength to high formability. Based on this type of new metallurgic concept, this research led to the development of new thermal processing technology using warm--reducing ¡Ý the world¡Çs first ¡Ý to achieve mass production of first-generation, electrical resistance welded steel tube with the conventionally difficult compatibility of strength and formability achieved.
- 2) Microstructure and Texture Control
- (1) Grain
With warm-reducing, grains were refined and high strength obtained due to a new mechanism for continual recrystallization of ferrite, as shown in Photo 1. For that reason, Cu, Cr, Mo, V, Ti and other special elements were not needed for achieving high strength for the HISTORY tube, resulting in superior recyclability. In recent years, R&D on similar grain has been undertaken in the STX-21 Project of National Institute for Materials Science, Material Engineering Laboratory and in the supermetals projects of Ministry of Economy, Trade and Industry and The Japan Research and Development Center for Metals.
- (2) Dual-phase fine dispersion (cementite online spheroidization)With the HISTORY tube, as shown in Photo 2, cementite spheroidization and fine dispersion occur in the warm- reduction state. Warm- reduction makes it possible to complete spheroidized annealing, which takes dozens of hours with hot-rolled strips, in just a few seconds, enabling manufacturing energy to be reduced.
- (3) High £ò-values
As shown in Figure 4, with the HISTORY tube using the rolled texture from warm reduction, £ò-values about 2-4 times higher than those of hot-rolled steel can be obtained even for low-carbon steel, high-carbon steel, dual-phase steel, and stainless steel, for which high £ò-values are difficult to obtain with steel plate utilizing the conventional recrystallized texture. From these results, it is indicated that the HISTORY tube has remarkably good bending formability.
- (4) Dual-phase structure
With warm-reducing, through appropriate control of rolling temperature, dual-phase structure for ferrite, martensite and the like can be comparatively easily achieved. With the HISTORY tube, high-strength, high-formability materials like those indicated in Table 1 can be obtained.
Research Prospects
The HISTORY tube is outstanding in terms of its high strength, high formability and recyclability. Study of its application as steel for automotive parts, as shown in Figure 5, is underway. Such application could make it possible to substantially reduce the weight of automotive parts on the order of 20% to 30% and could conceivably make a substantial contribution to improving mileage. In addition, the energy savings for manufacturing the HISTORY tube could be as much as 6% to 15% compared with the conventional hot- reducing method and other thermal processes. In this way, the HISTORY tube not only provides economic advantages but is also environmentally sound and is expected to contribute to global environmental protection henceforth.
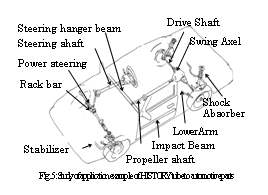